Upstream Data Inc. specializes in the design and fabrication of Ohmm bitcoin mining datacenters for stranded energy applications in oilfield. Our goal is to help oil and gas producers increase their bottom line by offering them profitable energy conservation options.
Opportunity
In July of this year we had the good fortune to commission an exciting project with a local oil and gas producer who had recently trialed one of our Ohmm Combo datacenters as part of our ‘Conservation as a Service’ offer.
For this project we were able to deploy the Ohmm Mini, our newest datacenter product, for an application that was a perfect showcase for what our technology is capable of.
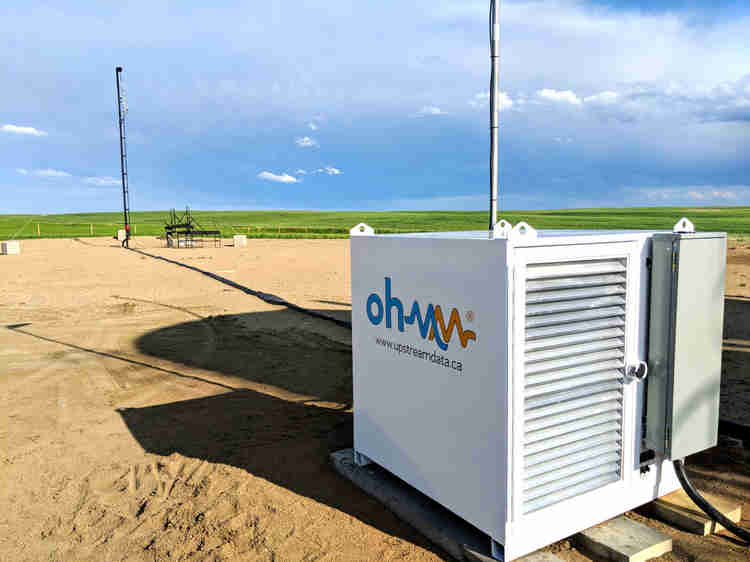
Snuffing the flare: Our prototype Ohmm Mini is operating in eastern Alberta. The flare stack in the background was decommissioned and is ready to be redeployed after all the waste gas was conserved. Picture taken July, 2019
Background
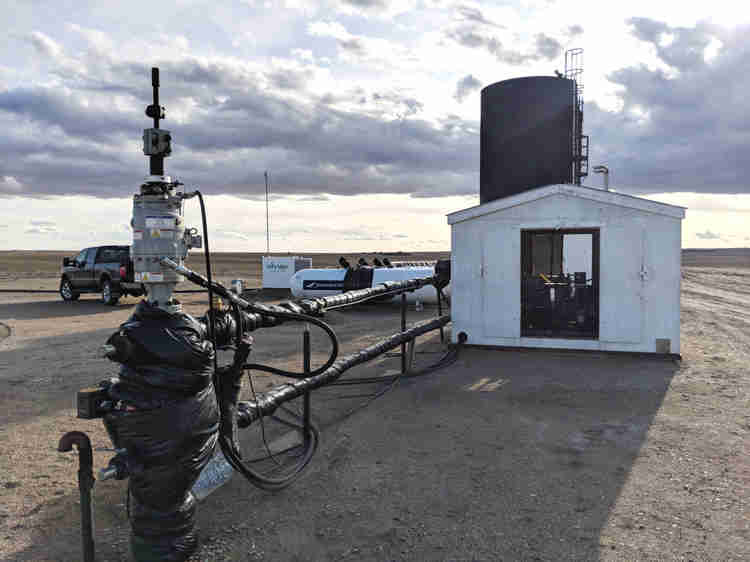
A beautiful heavy oil single well battery near the land of the living skies.
The producer had recently completed a new heavy oil horizontal well as the first drill of a planned multi-well facility. The site was equipped with a single natural gas aspirated 5.7L V8 Chevrolet engine fueled by the produced solution gas. The engine was coupled to a hydraulic pump which was used to drive the downhole pump – a rotary progressing cavity pump common in heavy oil production facilities.
Facility Production:
- 15 m3/day (94 bbls) total fluid , 60% BS&W
- 450 m3/day (15 mcfd) produced gas
Energy wasted up a flare stack.
This well site is located in an undeveloped and remote field and the usual conservation options, such as pipelines or power lines, were not an option. As a result the producer had no other option but to vent any excess gas that wasn’t being used as site fuel or dispose of it in a flare stack. The producer had a surplus flare stack in inventory and chose the responsible option and burned off the excess.
Engine operating under-loaded.
Since initial production rates were relatively low the engine only needed to use 10-15% of its rated output to lift the oil to surface. While over-sizing engines is standard practice to allow for upset conditions, operating engines under-loaded can result in frequent, costly maintenance events and shorten an engine’s useful service life. An additional problem is that low combustion temperatures will typically result in incomplete chemical reaction and a higher rate of polluting emissions.
Ohmm Mini Datacenter
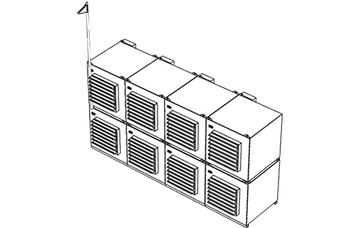
Multiple Ohmm Mini datacenters can be stacked and racked to conserve any energy supply. Individual Minis are easily redeployed as needed.
We designed the 50 kW Ohmm Mini datacenter to be a small, power dense bitcoin mine that could be connected to consume wasted natural gas on practically any oil and gas facility in the industry.
Each Mini is rated for 50 kW, enough load to conserve 450 to 500 cubic meters of gas per day, or 18 thousand cubic feet.
We designed the 4’x4’x4′ enclosure for easy transportation and installation. A single Mini can be paired with our 50 kW natural gas genset option, or if a producer has a larger power source then power can be split to feed multiple units. The enclosure design allows for multiple Minis to be be stacked and racked two-high and placed directly adjacent to each other to ensure a small, power dense footprint. The modular nature of the Mini allows producers to redeploy units to new sites as needed in response to depleting gas rates.
Each Mini consists of a basic or controlled option, both of which include a VFD that drives an exhaust fan based on the inlet temperature of the datacenter. An optional control package consisting of a PLC and power relay panel controls the total load of the datacenter. This way the datacenter will not overload the engine and knock it down during upset conditions such as fuel supply shortages or production over-loads. The datacenter babysits the engine and can reduce load any time it starts to sag, keeping it from power bumping and shutting down. This is particularly important if the engine is also the prime mover for other facilities.
Waste gas conservation
In July of 2019, after having trialed our Combo datacenter over the winter and validating its use as a conservation option and revenue generator, the producer was excited about the potential applications. The beautiful part of investing in an Ohmm mining datacenter is that none of the capital cost is sunk. Unlike pipelines or power lines, our datacenters can be redeployed as needed.
We worked with the Operations Foreman to execute the plan of pairing the Mini with an under-loaded engine in order to consume the excess gas and optimize the well site.
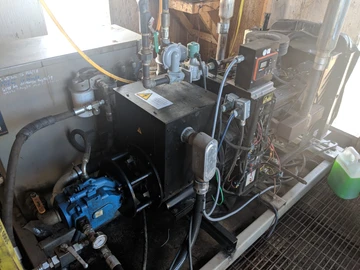
A Stamford thru-shaft generator is shown installed in between the hydraulic pump (blue) and the 5.7L V8 Chevy natural gas engine.
Since their existing engine was already coupled to a hydraulic pump we needed to first upgrade it to generate electricity. The producer installed a thru-shaft generator between the drive shaft of the engine and the hydraulic pump, which allowed them to generate electricity and continue operating the hydraulic system.
After mobilizing and spotting the Mini in place on site with a picker truck, our electrician tied in the Mini to the generator. Since we had already programmed it at
the shop all we had to do was flip the breaker on site and the producer was mining bitcoin and conserving waste gas at the same time!
The producer had chosen to start with 19x Antminer S9’s – the bitcoin mining processors – which added approximately 20 kW of load to the engine, bringing it up to approximately 60% of its rated output. The added load also allowed the engine to conserve the gas that was previously wasted at the flare stack, about 250-300 cubic meters per day.
Our sizing calculations were accurate and the extra load on the engine by the Antminers consumed all of the excess gas that was previously being flared. With the flare stack snuffed out, the producer can now redeploy it to a new well site, saving costs on a flare stack installation, worth up to $28,000 in equipment and labor.
Designed for Oilfield
One of the primary design goals of the facilities engineer is to build something that is operator friendly with minimal disruption to the existing production facility. Having spent much of my career optimizing oil wells, I have become hyper-focused on designing solutions that are modular add-ons to existing operations and are minimal overhead to the well site operators.
Every Ohmm datacenter has the option for a control package which enables automated load following and remote control. The control package prevents the mine from knocking down the engine by switching off circuits in response to over-loads. In this way our Ohmm datacenters will never upset the existing facility operations.
Conserving together
At Upstream Data our primary objective is to offer a conservation option to oil and gas producers. Having a background in optimizing production and facilities, we understand how to design operator friendly products and we are constantly interested in working with producers to improve our service. We are excited to work with producers to solve their stranded energy problems, so if this case study reminds you of a stranded gas problem in your portfolio then do not hesitate to contact our sales team and request a quote today!